Creating a 3D printable model
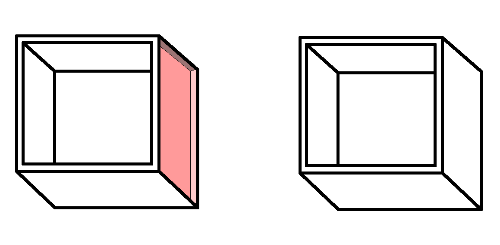
What does a 3D model look like?
The currently common file to save 3D models is STL - an abbreviation for StereoLitography. The company 3D Systems created this to be able to describe three dimensional objects.
An STL file contains triangles and a normal describing where the upper and the lower side of the triangle is. We call these triangles faces - they have one outer and one inner side.
The more triangles an item has, the larger the corresponding STL is.
Other formats describing 3 dimensional items also exist which provide additional information to just the geometry and whether a face looks inwards or outwards. Other formats like OBJ allow saving colors of faces or information about the roughness of the surface. But these formats are less common.
What does a 3D printable model need?
To have create a model that is 3D printable, some certain cirteria have to be met.
Enough walls
Most importantly, it needs to be a whole item.
Whole in this context means that it should not have open sides. We call this watertight. In short, this means that it needs to be compact and must not have holes where water could run in. Since all sides of a 3D model for printing have insides and outsides, all outsides should face outward and all insides should face inward.
This can be compared to for example a thermal or vaccum flask keeping your tea warm. It has an outside wall and an inside wall where your tea is inside kept warm. In case there are holes in the walls, the tea can leak into the thermal flask.
In case you draw something virtual, it can easily happen to forget that things in the real world have outsides and insides, even very thin things like a sheet of paper has a thickness as everything has in the real world. In case you forget sides, we can not get your item into the real world without repairing it.
Thicknesses
A walls thickness should never be below the printing nozzle or minimum material grain size. Also it should be thick enough to withstand whatever you think it should be used for. In case you create thinner walls than what physics and material gives us, the machine will try to fullfil your wish by making unexpected things during printing.
Always separate walls
Intersecting walls are no problem as such, most software can handle this. However, intersecting walls are no good news. It means that two walls are stuck into each other which you can do in a virtual environment but in the real world, sticking things into each other like needles into fabric creates holes. In the virtual world, it is just two objects in the same space. Try to avoid this, it can cause calculation errors and lead to quide unexpected results.
Filesize
The more faces a model has, the larger the file that is loaded into the printer. Often round shapes have many faces. However, large files can be a problem for the printer software or the computer that generates the information so the machine knows what to do. Please try to keep the file size under 30 MB, about 5 MB would be optimal.
The larger your item, the longer the calculations will take and the more errors may occur. 3D slicing (cutting your item into slices that are printed one after the other) is a complex mathematical process, and the more data you have to calculate, the harder it will be for the computer to calculate it. So, for example, avoid things that are unnecessarily "round". Round in the sense of: Every 3D model is usually made up of triangles, and since round shapes are only ever mimicked by angular things that triangles just are by definition, it is not necessary for your object to be rounder than a human can see or perceive as round. So keep it to a resonable minimum.
Connected walls
Sometimes it happens that models are created that to not combine the parts of the model into one single model. Thiy can often be handled by printing softwares but it would be the equivalent of you putting on clothes. They are not really part of you, just on you. This can confuse machines sometimes.
Thus, a proper 3D printable file should have all parts connected to be one single and complete shape - like your skin is totally attached to you.
How can I create a 3D model from scratch?
In case you would like to create your first 3D model, you can use a wide variety of software to do that. They all have a different focus and you can choose whatever tool suits your task best.
Tinkercad
Very easy to use is Tinkercad by Autodesk (free to use) that also allows you to learn about basic 3D model creation and even produce your own lectures. When working with this tool, make sure you always look at your working area from multiple sides. Since screens are flat, it is hard to detect where in a three dimensional environment your object actually is. There is also a way to collaboratively work on a project simultaneously.
https://www.tinkercad.com/
GeoGebra
GeoGebra allows users to create objects using mathematical equations or formulas. In case you already have an account, you can use this feature. If not, we encourage you to check out GeoGebra which focuses on aiding teachers primarily in the STEM area and of course it is also free to use.
https://www.geogebra.org
OpenSCAD
Another free tool that is widely used by teachers and students with a more intense background in informatics is OpenSCAD. Here, you basically program your 3D design. This is often the choice for generating items with varying variables like a generator for bracelets that makes different shapes every time you run it.
https://www.openscad.org/
https://www.openscad.org/cheatsheet/
Examples on Thingiverse are available! Most customizers are done by OpenSCAD. https://www.thingiverse.com/thing:1485673
Google SketchUP
There are free and proprietary versions of SketchUP. Some improved versions are also free for schools after registrations. As Tinkercad is, this tool needs a connection to the internet since it relies on the cloud. Since also 3D printing is supported, it comes with some basic shapes just as SketchUP does.
Blender
Far more complex but still free is Blender which was not primarily a tool for generating printable 3D items but for creating 3D models for computergames. The vast array of different settings can be very confusing for beginners. However, working with Blender has many advantages when it comes to evaluating your 3D designs physical attributes.
Fusion360
This tool is free for academic use but costs in case it is used in a proprietary environment. Using this tool, we are back in the array of tools from Autodesk. Again, this tool contains an array of different options that can be confusing for beginners. The focus of this tool, however, was not creating items for computergames but designing CAD drawings. It is thus widely used by people who both want to learn about CAD and 3D modeling.
FreeCAD
FreeCAD is a relatively simple to use CAD drawing program that also allows you to export STL files which you can use for printing. This tool is free as the name indicates. Since CAD drawings are not per se meant for printing, it is advised to have the resulting STL repaired before printing.
Rhino
Very commonly used by 3D designers is Rhino. A licence for 30 students varies between 400 and 1000 Euros.
How can I turn an existing item to a 3D model to print?
Existing objects can be turned into 3D objects using some sort of scanning it.
Usually, this is done by a process called photogrammetry where many pictures of all sides of the object are put together to shape the object. For this, it is necessary to have as many pictures as possible from the same distance to the object. Otherwise, details could be interpreted as too big or too small that they really are. Also, the objects should always be very well lit so all details can be visible on the images.
The pictures can come from scanner systems which usually come already with the software putting together the object or from other sources like extra scanners, cameras, or smartphones. However, often they need extra software which can cost alot additionally.
Scanning with smartphone apps often costs per data export or have a monthly fee and a good scan needs some experience in moving the smartphone in exactly the right distance at the best speed around the object.
How can I repair a model?
There are several approaches to checking a 3D designs printability and repairing it in case it has the need for improvement.
One very simple solution - in the case of already having an Autodesk account due to using TinkerCAD - is the Netfabb online service.
Simply upload your 3D design to https://service.netfabb.com/login.php and get them back as repaired as possible. This service connects walls and closes holes.
However, to avoid unexpected results, check your file before you press the print button once more. Sometimes, repairing can have unwanted side effects.