Propulsion and Machines
An Internal Combustion Engine
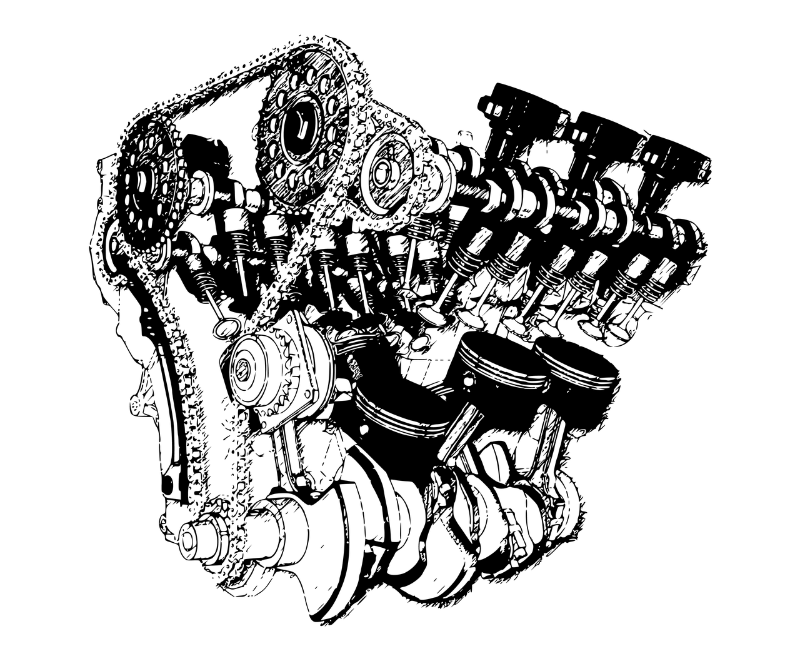
Vehicle Propulsion
When you look around these days, we have two main forms of propulsion that drive the vast majority of our vehicles around the planet - internal combustion engines and electric motors. The latter are becoming more commonplace than even a decade ago, but are still greatly outnumbered by the former.
While it might seem that it should be simple to substitute an electric motor for an internal combustion engine, it turns out that the way they deliver the force that propels a vehicle is very different.
Internal Combustion Engines
An internal combustion engine burns gasoline, diesel or something similar (like E85) which combusts, in order to produce heat. The heat causes air inside the combustion chamber to expand against a piston which in turn rotates a crankshaft which goes through a transmission and eventually the wheels turn.
From experience you probably know what it means to start an engine. If an internal combustion engine isn't turning, it is off. In order to produce any force, it must be turning. If it wasn't for some details of air flow into and out of the engine, an engine would produce the same force to propel your car regardless of engine speed. In reality, the effectiveness with which the engine sucks air into the combustion chamber as well as the flow restrictions typically lead to a force that at first rises with engine speed and then after moderate engine speeds decreases due to flow restrictions.
Ultimately what puts an end to an engine spinning ever faster is that the engine needs to "inhale" air to mix with the fuel for combustion, and then needs to "exhale" that same air with spent fuel out the tail pipe. It is the flow of air through small intake ports and exhaust ports that becomes very difficult at high engine speeds. Quite literally the energy of combustion ends up being entirely wasted on the intake and exhaust of air at too high an engine speed and none is left over to propel the vehicle down the road.
An example can be seen below. The lower curve is labeled as "torque", which is the effective twisting force of the crankshaft. While it comes out of the engine as a torque, or twist, when the rubber hits the road it is just a force to propel the car. Please don't misunderstand this to mean that torque equals force. It doesn't. But after the torque turns gears and drive shafts and wheels, what we get is a force that is proportional to the torque. The effect of gearing is discussed later.
Modeling a Torque (or Force) Curve
If we wanted to define a function that looks like a torque curve, we could use a polynomial function to fit to the curve. That is the most common thing to do. The simplest function that seems like it might fit the curve is a downward facing parabola, but that's a bit too crude. In GeoGebra, photos can be imported. The image of a torque curve is imported and scaled correctly below. Points are then created that fall along the curve, and a polynomial curve fit (3rd order) was made for the set of points. In the example seen below the points can be moved and the effects can be seen in real-time on the curve fit.
Example of Fitting Image of Torque Curve
Electric Motors
An electric motor uses the energy stored in batteries or from a power grid to generate electric and magnetic forces which in turn create rotation that serves to turn gears and drive a vehicle. The characteristics of the force generated are very different from those generated by an internal combustion engine.
The maximum force generated by an electric motor occurs at zero speed. The faster it goes, the less force it can generate. The reason for the decline with speed is for completely different reasons than in an internal combustion engine. We will have more discussions about electric motors during second semester, but here are the basic ideas: Electric motors are also electric generators because of the way natural law works. We can use the voltage from batteries to turn a motor, and turning a motor will generate a voltage. The trouble is that the generated voltage is always fighting the effects of the battery. The faster the motor turns the more it fights. At a high enough speed the generated voltage completely cancels the battery's voltage. This is called the no-load speed of a motor. The motor can not turn any faster than this on its own.
The upside to this effect is that the faster the motor turns, the less current and energy it draws from the battery - something which we'll work out in our studies of electromagnetism. On the other hand, at zero speed the motor draws maximal current and energy from the battery. This is in direct contrast from internal combustion engines which can't burn any fuel when they aren't moving, and burn it quicker the faster they are running.
The specific shape of the force versus speed curve for an electric motor is shown below. It is very nearly linear. The y-intercept is the stall torque, which relates to the maximum force it can generate, or stall force. The x-intercept is the no-load speed discussed above.
Electric Motor Force Vs. Speed
Gearing's Effect
The effect of gears that sit between a motor and the wheels is to make a trade off between force and speed. The product of force and speed is determined by the motor. If you need more force, it will always be at the expense of lower speed potential. If you wish to go faster, it will have to be at the expense of having a lower force with which to accelerate and push the wind out of the way.
This is true in general, not just for electric motors. If you wish to experience huge force with which to accelerate a car, it will be in first gear. While the force is large, the gear probably can't propel the vehicle beyond 35mph or so - depending on the vehicle. Second gear will get you going faster, but at the expense of having a weaker force with which to propel the car along.
The graphic above shows this effect on the force curve. You can change the stall force and see its effect on the no-load speed.